- Products
- Markets
- Services & Tools
- Newsroom
- CSR
- Blog
- We are Nexans
- Search
- Contact us
- Compare
- Sign in
The burning sun at cables: How are UV-resistant cables build?
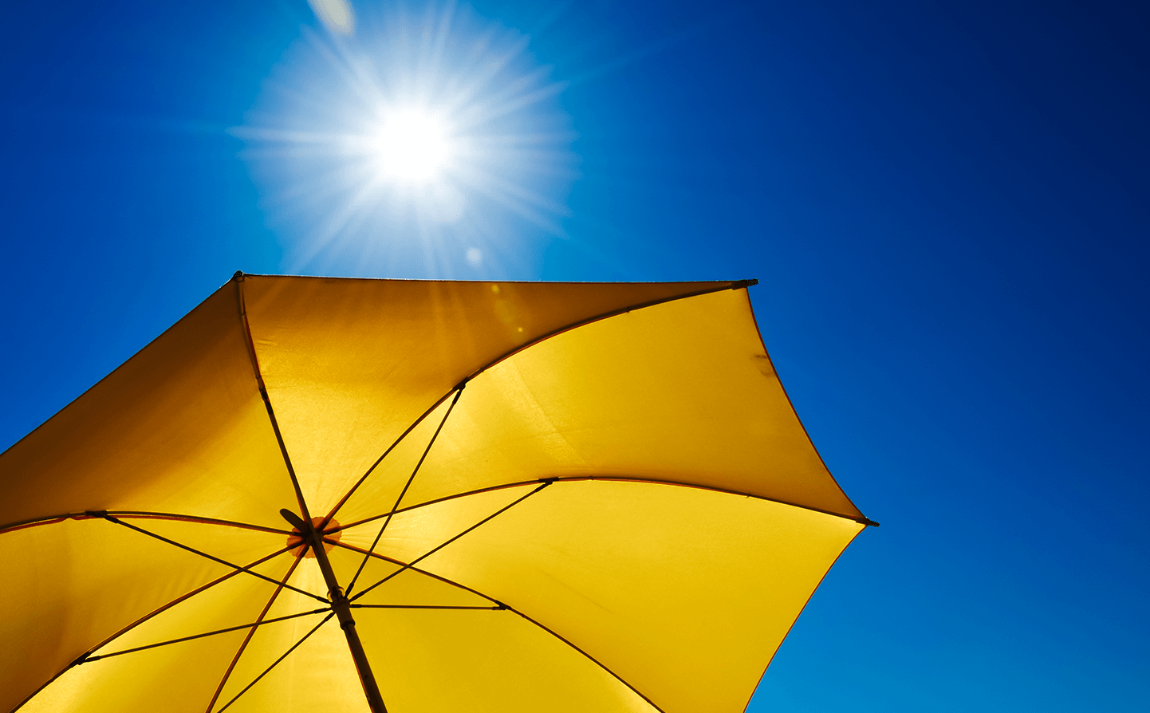
We all know what effect Ultraviolet (UV) radiation from the sun has to our skin, but do you know what effect it has on cables and wires? Fortunately, all of our installation cables are UV resistant, but what exactly does that mean? You'll find the answers to these questions in this blog.
A UV-resistant cable is a cable specifically designed to resist the harmful effects of ultraviolet (UV) light. Just as UV light can be harmful to our skin and eyes, it can also damage cables. Prolonged exposure to UV light can break down the outer jacket material of the cable. This allows moisture to enter the cable, which can result in short circuits and equipment failure, causing potential safety hazards
How are UV-resistant cables produced?
UV-resistant cables are made by using special materials and techniques. Here are the steps typically taken to produce UV-resistant cables:
- Choice of materials: UV-resistant cables are manufactured using materials that are naturally more resistant to the harmful effects of UV radiation, including EVA, PVC or PE-based plastics.
- Addition of UV stabilizers: To improve UV resistance, UV stabilizers are added to the material. These additives help absorb and break down harmful UV radiation before it can damage the material.
- Construction and shielding: Some cables are constructed with multiple layers, including insulation and shielding layers. These layers not only help protect the conductors, but also provide additional protection against UV radiation.
- Quality control: During the manufacturing process, the cables are subjected to rigorous quality controls to ensure that they meet the required UV resistance and performance standards.
The end result is a UV-resistant cable that is capable of being exposed to UV radiation for long periods of time without affecting the performance and integrity of the cable. The level of UV resistance can be determined through testing following harmonized testing standards such as EN 50289-4-17.
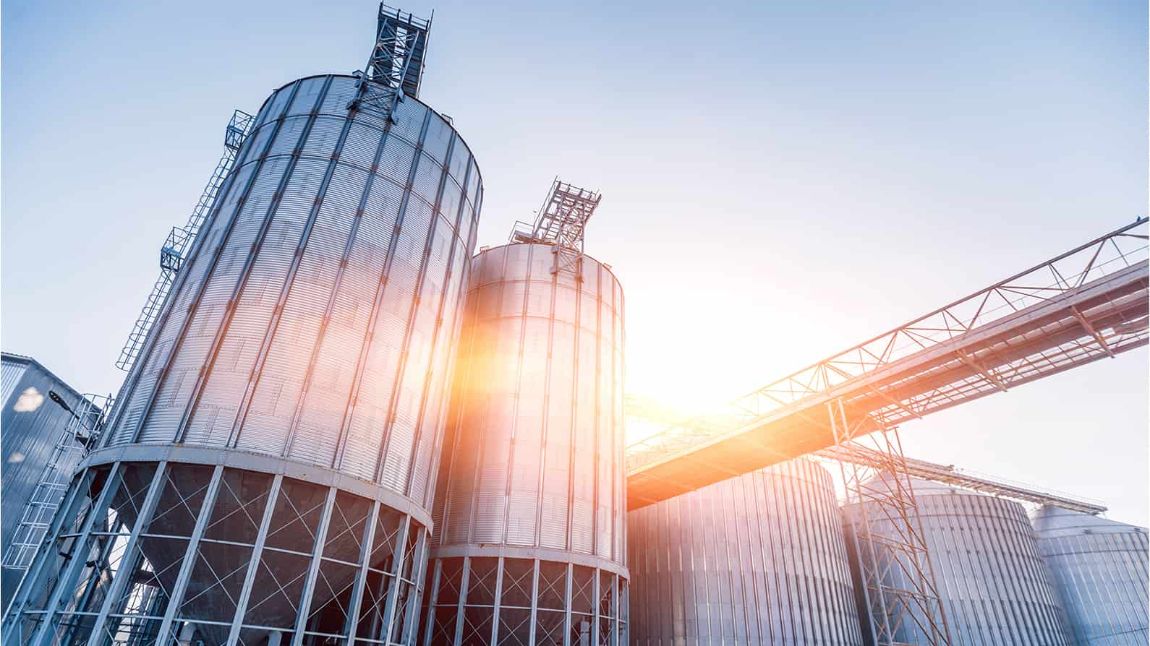
In what areas are UV-resistant cables and wires used?
UV-resistant cables are mainly used in outdoor environments when the cables are directly exposed to sunlight. Charging cables of electric cars, cables that transport solar energy from PV modules towards buildings, or cables running to satcom dishes. UV-resistant cables are also needed in road and rail infrastructure, on construction sites or in large industrial plants.
In addition, UV-resistant cables can also be useful in certain indoor applications, such as in the pharmaceutical industry where equipment is sterilized using UV light. These cables ensure that UV light can be used safely without damage to the cables and wires.
Nexans cable offers UV-resistant cables by default
Our installation cable range complies with the 720 hours test according to test standard EN 50289-4-17 Method A, making them perfectly suitable for outdoor use in our Dutch climate.
This applies to our standard cables in fire class Dca such as YMvK Dca, but also the halogen-free cables such as ALSECURE YMz1K Cca and ALSECURE YMz1K B2ca are fully compliant with this test standard. These cables have improved fire response while not compromising on ease of use. When protecting lives and sensitive electronic equipment is important, choosing the right cables is essential.
Nexans halogen-free cables emit less toxic smoke in the event of a fire, facilitating evacuations and reducing additional smoke damage to expensive installations. They are suitable for use in installations in industrial, residential and tertiary environments.
Our websites
Select your country to find our products and solutions
-
Africa
- Africa
- Ghana
- Ivory Coast
- Morocco
- North West Africa
- Americas
- Asia
- Europe
- Oceania