- Products
- Markets
- Services & Tools
- Newsroom
- CSR
- Blog
- We are Nexans
- Search
- Contact us
- Compare
- Sign in
Practical sustainability
Reducing our ecological footprint
We invest heavily in sustainability to make a real difference. So, what is Nexans actually doing in practice? On this page you can read about the measures we are taking, the services we offer, the projects we are launching, and the collaborations we are engaging in to promote sustainability. Because promises alone won't make the planet sustainable.
- Maximising the recycled contents in products:
- Recycled copper;
- Recycling of plastics;
- Preventing environmental pollution in our factories:
- Limiting the use of energy, water and raw materials;
- Strict environmental requirements to prevent pollution;
- Accessibility of emergency intervention kits and frequent practice drills on all our production facilities;
- Reducing CO2 emissions:
- By producing smart with regional production;
- By using more sustainable energy;
- By taking energy-saving measures.
Copper and other non-ferrous metals
Most cables contain conductors of copper or aluminium. The production of new non-ferrous metals have an impact on the environment. That is why Nexans aims to maximise the proportion of recycled copper in its cables. The benefit of this is that we can use our own copper metallurgy, with foundries in Lens (France), Canada and South-America. This contributes to the global reduction Nexans' carbon footprint and limits the dependency on natural copper sources.
Currently (2023), Nexans mixes around 5.4% of recycled copper with new 'bare' copper, and with the support of our R&D department, our foundries are working hard to increase this percentage even further. The foundry in Lens has set the goal to process 30% recycled copper in the copper it produces by 2030!
During the production of copper, a large amount of CO2 is emitted. Nexans focuses on restricting these emissions by improving production processes and transport, among other things.
Objective for 2030
Our foundry in Lens aims to increase the amount of recycled copper in new production from 14% to 30% by 2030!
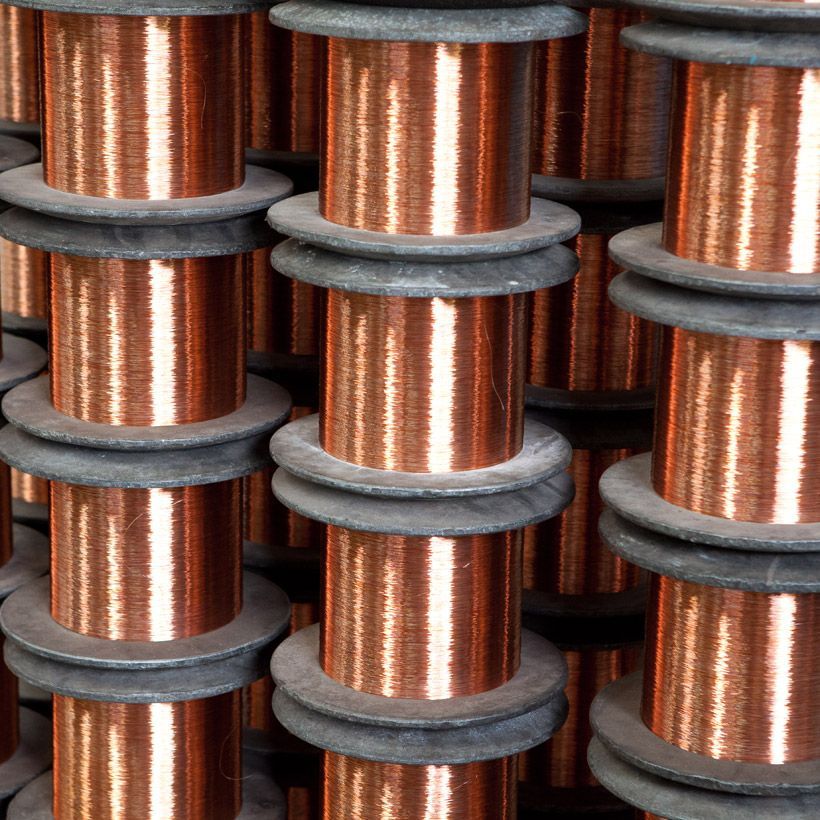
The worldwide demand for copper keeps increasing and is estimated to rise to 40 million tonnes of copper by 2030. The market of secundary (recycled) copper is still stuck on around 9 million tonnes of copper. New copper will unfortunately still be needed for the time being.
Recycled copper comes from urban mines, like cables from old constructions. Technically, it is challenging to obtain completely pure copper, which can result in minor impurities. For cables with 100% recycled copper this can result in cables that do not comply with the standards. In short, only a small part of the secundary copper is suitable for these cables. Globally, there will be demand for this limited supply from many countries, which will drive up prices.
That is why Nexans chooses to maximise the percentage of recylced copper in regular cables.
Recycling of polymer waste
There are different initiatives to better recover plastic waste, like PVC, PE, XLPE and filled polymers. The goal is to switch to a more circular model, in which materials are being reused in the production of cables. In 2023, significant research was conducted on the recycling of XLPE and elastome waste.
Recycled polymers are also used in packaging, like Mobiway cable drums, made of 100% recycled polypropylen, and packaging foil made with 30% PCR recycled plastic.
Biobased material in cables
In the cable industry, there is currently a rise in biobased materials, like biopolymers made of soy. Biobased material has less adverse consequences for the environment than regular plastics made of petroleum. However, there is still a huge lack of clarity about the long-term environmental impact and life span, which is why Nexans still makes very limited use of biobased materials.
In 2022, Nexans started an extensive global technical study, to map the opportunities and properly test potential materials. We focus on:
- Technical qualities: does it have the right mechanical qualities, is the long-term quality ensured and does it meet the product standards?
- Scalability: can sufficient quantities be produced for large-scale production?
- Environmental impact of the materials: is the environmental benefit in the life span demonstrably positive?
On the other hand, the production of biobased also has downsides:
- Soybean cultivation plays a part in the deforestation of the rain forest;
- The construction of soybean fields often involves significant CO2 emissions;
- Soy is an annual plant and depletes the soil quickly, resulting in desertification;
- During production a lot of fresh water and pesticides are being used.
Nexans wants to prove that the use of biobased materials is actually benificial for the environment through Life Cycle Assessments.
Besides the environmental aspect there is also a discussion taking place about the life span of these biobased materials. Traditional cables have a long-life span, while the life span of biobased materials is still partially unknown. The reliability of future cables made of biobased material can be proved with solid research into:
- mechanical properties;
- waterproofness of the materials;
- if the product is affected by environmental influences.
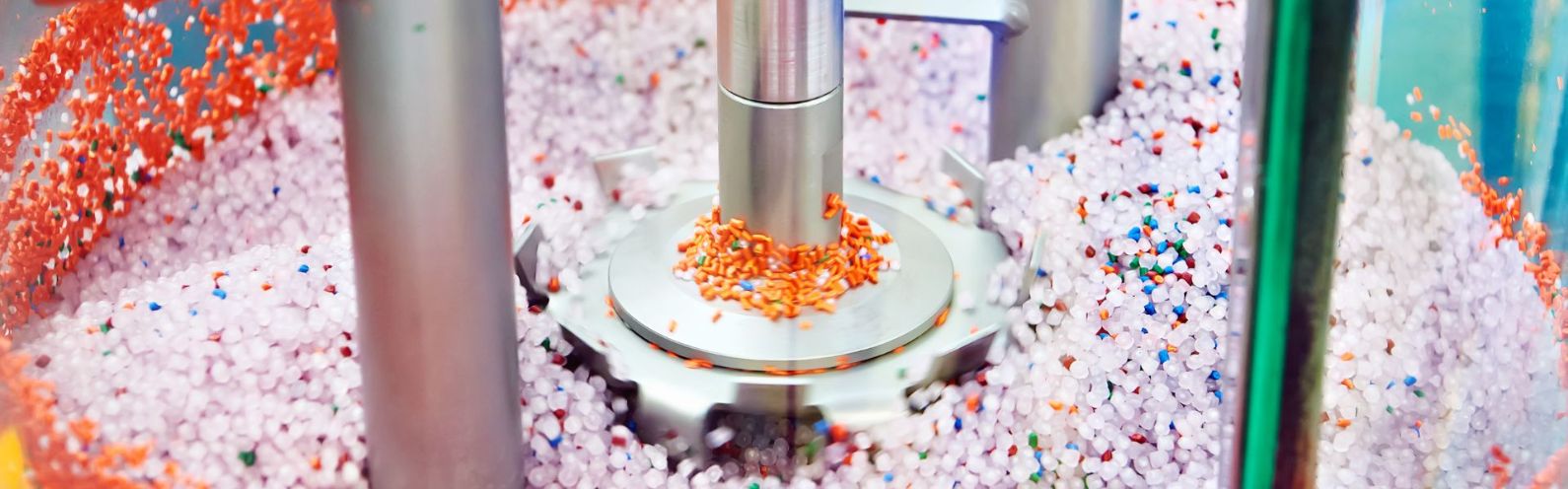
Constant vigilance against all pollution
The ISO 14001 certification and the corresponding audits contribute to our efforts to reduce the Group's environmental footprint and control its pollution risks. With this in mind, the Group analysed the sources of pollution produced by each of its business activities and has implemented numerous measures in compliance with regulations:
- Continuous casting: processing and monitoring of the smoke generated by continuous casting furnaces as well as storage and transport of hazardous materials (acid, etc.);
- Metallurgy: processing and filtering of emulsions used for wire drawing;
- Cable manufacturing: recycling of the water used in the extrusion process, filtering of air emissions and processing of solvents used for storage cabinets and extractor hoods;
- Compound production: implementation of specific measures at any sites that use pollutants such as peroxide, silane and plasticizing agents (e.g. ventilation and spill pallets).
Nexans has also implemented a series of initiatives designed to limit:
- Discharges into water networks: to prevent the risk of accidental spillages;
- Discharges into the soil: using containment tanks and emergency intervention kits to prevent spillages or gradual pollution;
- Air emissions: prevent air contamination through the use of particle filters (VOCs, etc.);
- Noise pollution and vibrations: keeping noise to a minimum through constant measurement, specific training and flexible working hours.
of Nexans sites are ISO 14001 certified
of Nexans sites got awarded by environmental certification
certified sites is the target for 2030
Reducing dangerous substances in cables
All Nexans products comply with legislation relating to chemical substances, in particular, the REACh regulation (EC 1907/2016) and the RoHS directive (2011/65/EU) to better protect human health and the environment. Nexans has set an annual target to eliminate dangerous substances, which is to be achieved by implementing a dedicated roadmap and action plan.
Crisis management plans for the environment
All sites within the Group must draw up an environmental crisis managment plan which must be regurlarly audited and backed by investments in protective equipment such as:
- containment basins and valves to prevent pollution from outside the site;
- emergency intervention kits (contaminant booms, mobile valves, etc.).
This equipment is tested during dedicated verification exercises, so they can be used effectively in case of emergency.
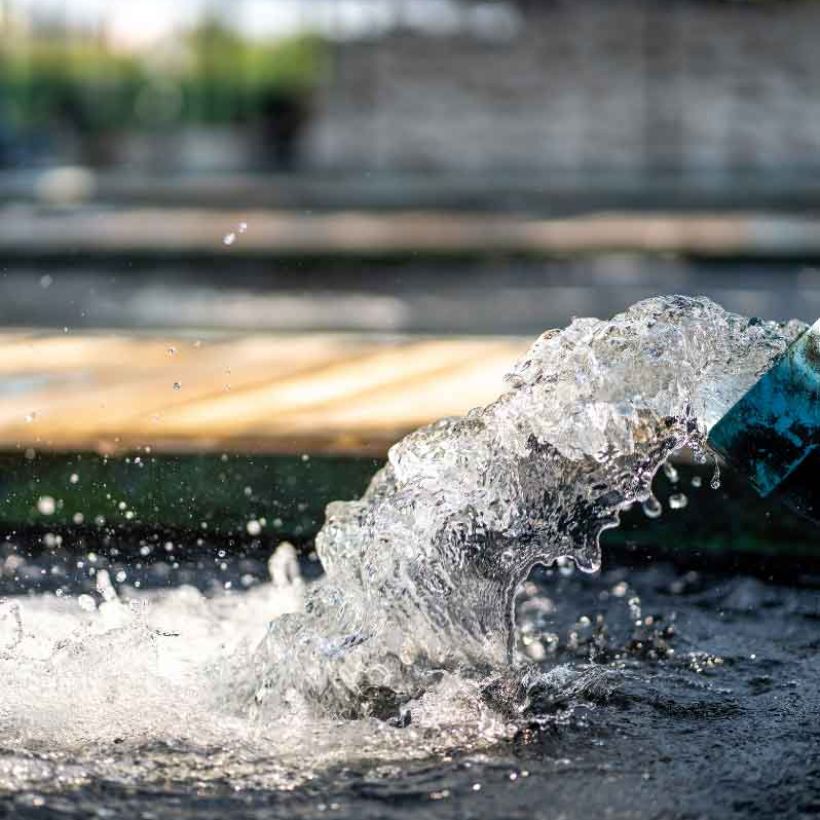
Nexans invests in closed cooling systems and monitors sites with high water consumption. Since 2020, additional tools and resources have been added to more accurately monitor the water use and a test with leak detectors on gauges has started for improved water management.
In our plant in Buizingen (Belgium) rainwater is being collected and used as cooling water in a closed system, effectively reducing the environmental impact.
Water recycling rate for 52% out of the 55 sites using cooling operations.
of recycled copper in 2021 (compared to 24,000 in 2020), melted in the continuous casting processes of Montreal (Canada) and Lens (France), i.e. approximately 5% of our factories’ requirements.
Reducing greenhouse emissions
For the production of cable a lot of energy is necessary. A dedicated working group at Nexans is actively working on measures to save energy and reduce CO2 emissions. This includes the purchase and/or production of renewable energy and measures to work more energy efficient.
There is a quarterly registration system for energy consumption (electricity, gas and fuel) on all industrial locations to gauge the measures.
Measures have already been implemented at various locations:
- Energy efficient LED lights replace traditional lighting;
- Wind turbines have been installed in Buizingen (Belgium);
- Solar panels have been installed in Cortaillod (Switzerland) and Lebanon;
- nergie-efficiëntere LED-verlichting vervangt traditionele verlichting;
- In Grimsås (Sweden), the plant is heated using wood waste from old drums and pallets, replacing a previously used oil-fired boiler.
Transport
Thanks to our local production facilities in the Benelux, we can avoid a lot of transport miles. But there is still a lot to win. This applies to the transport of raw materials to the factories, as well as the efficient distribution to wholesalers and end customers.
In 2023, Nexans has started a pilot programme, as part of the French FRET21 project, to reduce CO2 emissions of cargo transport between the French and Belgian plants and their neighbouring countries. There is also a lot to improve in the load factor of transport. In Norway, specific trailers to transport cables on two heights have been used since 2022, resulting in up to 90% more capacity per trailer. This way, a sustantial reduction in transport movement can be achieved.
With the FRET21 project Nexans wants to reduce the CO2 emissions from transport between Belgium and France. Our three levers for action are:
- Loading rate: a higher filling rate reduces the number of journeys as well as fuel consumption;
- Responsible purchasing: favouring approved suppliers registered in the CSR charter of Nexans Suppliers, or bearing the “CO₂ Objective” label, we opt for suppliers who focus on sustainability;
- Means of transport: partially switching from road to rail transport, the energy combination favours the use of carbon-free electricity.
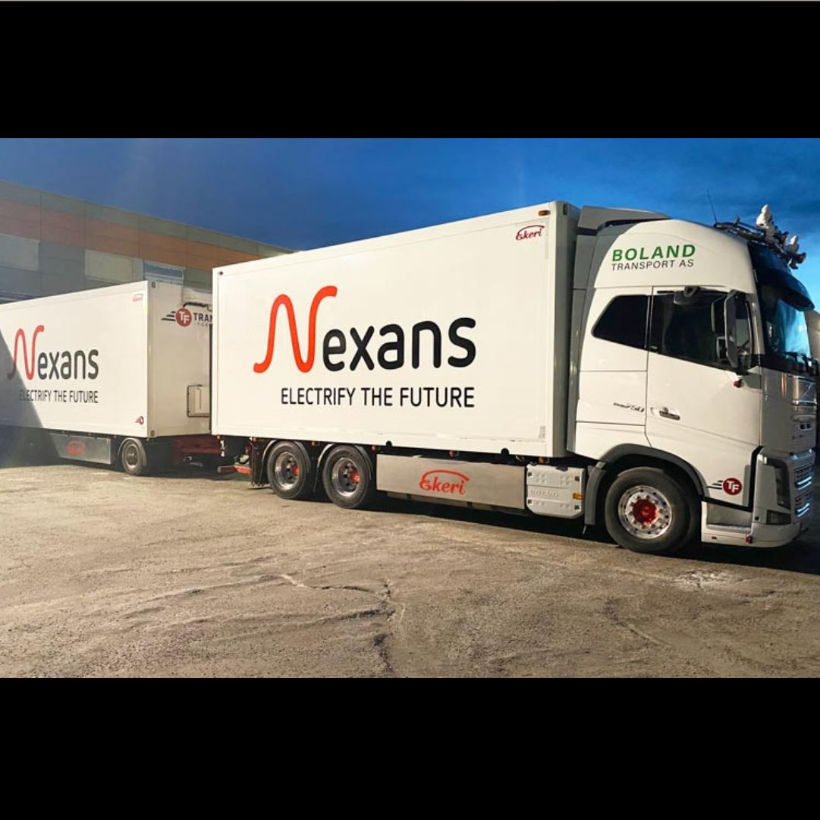
We provide useful tools & services that benefit the customer and the environment!
Our websites
Select your country to find our products and solutions
-
Africa
- Africa
- Ghana
- Ivory Coast
- Morocco
- North West Africa
- Americas
- Asia
- Europe
- Oceania